In a smart factory, the products control their own production processes
In the Swiss Smart Factory, the factory of the future is within reach. Here, Swiss industry can find advice on how to tackle the digital transformation. Head of Research Dominic Gorecky knows: There are still many hurdles to overcome on the path towards Industry 4.0.
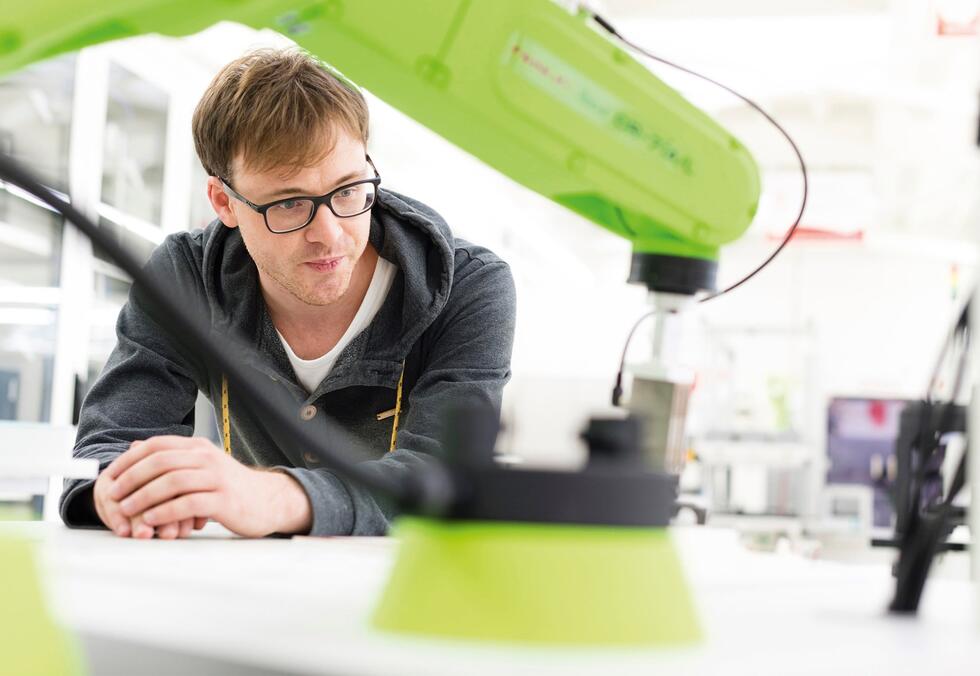
Dominic Gorecky picks up three digital dice. He shakes them, and a number appears on each one. Regardless of the order in which he lines up the dice, the third one always displays the sum of the first two. In the smart factory of the future, the networking of machines will be just as simple, Dominic Gorecky explains.
The German engineer has been specializing in the digitalization of production processes since 2009. He was the Scientific Director at the German Research Center for Artificial Intelligence and was Head of the SmartFactoryKL research laboratory in the German city of Kaiserslautern. Today he supports Swiss industrial companies with the networking of their production processes.
How well do present-day machines understand each other?
There is still a great deal of translation required. In the smart factory of the future, machines from all kinds of manufacturers will be able to communicate with each other. Although this is already possible today, it still requires a great deal of effort. Sensors have to be fitted, connectors have to be installed, and programming languages have to be translated. But I am convinced that the plug-and-play concept will also establish itself in the industrial sector. In the smart factory, a Japanese robot and a Swiss machine tool will immediately understand each other. After a brief introduction, they will be able to start working together. But this will only be possible if we agree on standards.
What will the factory of the future look like?
In future, we will no longer manufacture our products in huge factories, but in small, highly flexible production facilities that have a modular design. Expanding, moving, or replacing machines will be possible in a simple and quick process. The smart factory will be networked both internally and externally. It will be integrated into a logistics network and connected directly to suppliers and customers. The products will control their own production processes while taking account of specific customer requirements.
Does this mean that people will no longer be required at all?
I do not believe that machines will be able to organize their production processes completely independently in the foreseeable future. The goal is flexible automation that will take care of the burdensome work for us. Collaborative robotics, for example, can play a valuable role in supporting humans. However, the smart factory will also raise delicate sociotechnical issues. For example, what are the implications if production managers work together with artificial intelligence? Who has the final say, the human being or the technology? I believe it is important for the technology to be able to justify every decision and for the humans to retain the authority to make decisions in critical cases.
Much of what Dominic Gorecky says sounds very futuristic. But the Swiss Smart Factory in the city of Biel clearly demonstrates that the building blocks of the smart factory have long since become a reality: Objects communicate with each other via the Internet of Things (IoT), parts can be tracked seamlessly using Radio Frequency Identification (RFID), and collaborative robots work hand in hand with humans. Training courses are held using virtual reality (VR) and assembly lines are designed using augmented reality (AR).
At present, the Swiss Smart Factory is still a temporary solution. It is located on the outskirts of Biel next to a car dealership. And it doesn’t really resemble a factory. It looks more like a research lab for robotics students or a start-up run by tech geeks. But maybe this is precisely how we should imagine the factory of the future: A few 3D printers and a couple of robots producing everything our hearts desire.
The Swiss Smart Factory is a showcase platform, test laboratory, and competence center all rolled into one. Dominic Gorecky and his team are guiding the Swiss industry into the future and working together with companies to implement innovation projects. There is a great deal of interest in the exchange of ideas with the experts at the Swiss Smart Factory, not least because particularly for smaller companies, Industry 4.0 represents a huge project involving many challenges.
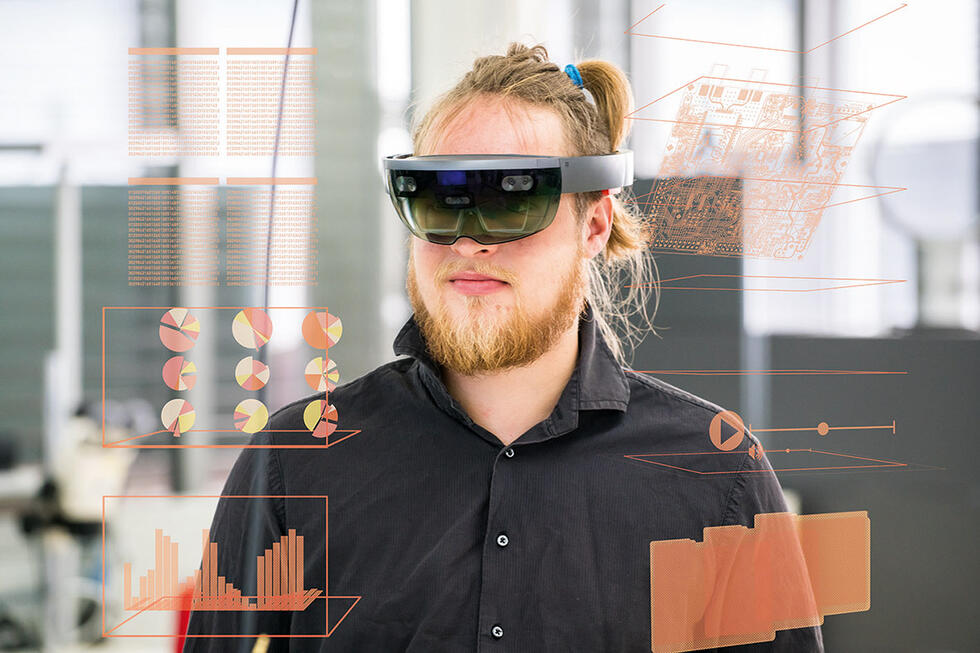
How much of the vision of Industry 4.0 is already a reality today?
Industry is currently undertaking its first steps, usually in the form of IoT projects. Many companies have also already prepared a roadmap for the digital transformation. But Industry 4.0 is a moving target that is constantly evolving, and the subject is too complex to tackle single-handedly. Networking with other companies is an absolute must. On the one hand, in order to jointly accumulate know-how, but also because networking is an integral aspect of the smart factory. This is why manufacturing companies have to become more open.
But is the industrial sector actually open enough for this process?
It is true that the industrial sector has always tended to be secretive. But in the meantime, a number of companies have realized that isolation is counter-productive. In Germany, for example, there are production facilities that are setting a good example in terms of Industry 4.0 and that are opening their doors, such as Siemens in Amberg or Bosch Rexroth in Homburg. But of course there are still widespread reservations against networking with other companies. Many industrial companies still believe that the risks outweigh the benefits.
And why are you convinced that the benefits outweigh the risks?
Because opening up enables us to collect information over the entire life cycle of our products, which in turn allows us to optimize the value chain. In this way, we can continuously improve our products and processes. Simultaneously, it enables us to strengthen customer loyalty. In future, customers will not only pay with money, but also with data. In return, however, they demand transparency and want to know how the products they use are manufactured. Thus, it is also the customers who will ultimately play a key role in forcing the industry to open up.
In the smart factory, a Japanese robot and a Swiss machine tool will immediately understand each other. After a brief introduction, they will be able to start working together. But this will only be possible if we agree on standards.
Dominic Gorecky’s team will soon move from the outskirts to the city center of Biel. At the end of 2020, with a total floor space of some 15,000 square meters, the Switzerland Innovation Park Biel/Bienne will open its doors right next to the main railway station. The new complex, which is intended to strengthen Switzerland’s innovative drive, will cost 45 million Swiss francs. The fact that it is being built at the heart of the Swiss watch industry is emblematic. The Swiss Smart Factory’s large, open shop floor will constitute the centerpiece of the Innovation Park. Thus, the factory of the future is set to become even more tangible.
Gallery of employees
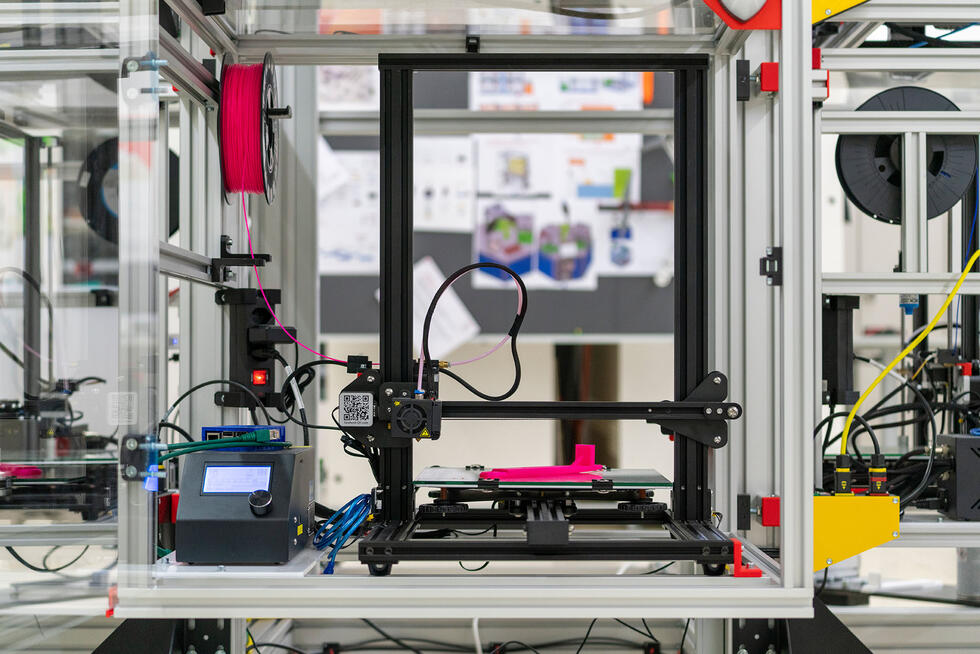
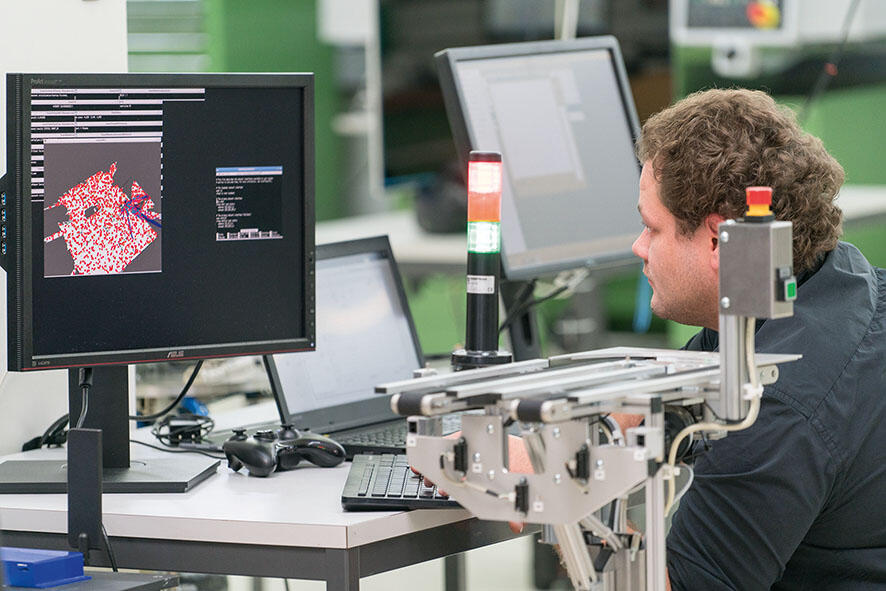
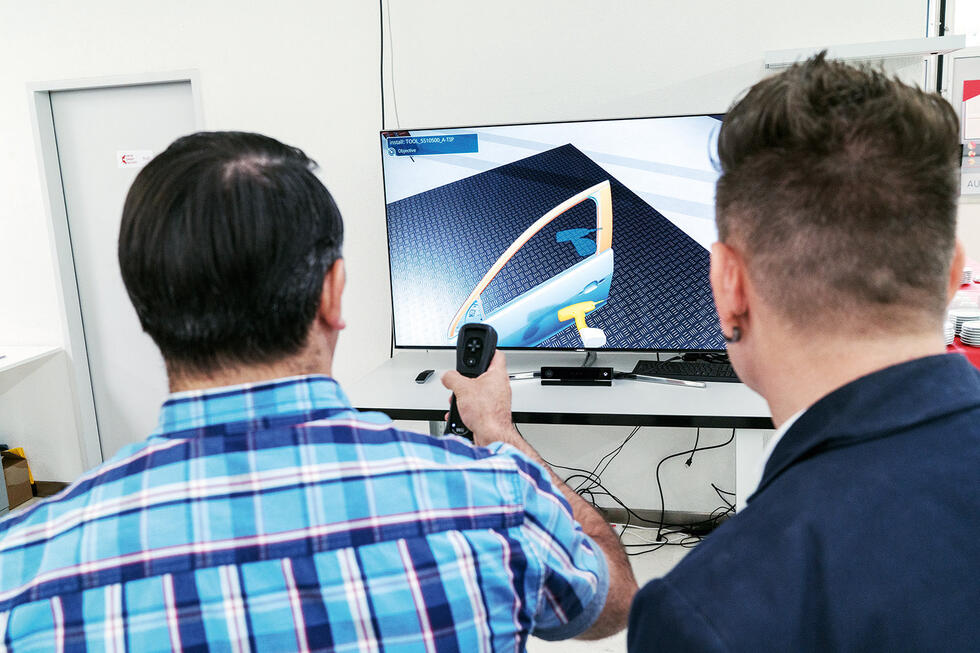
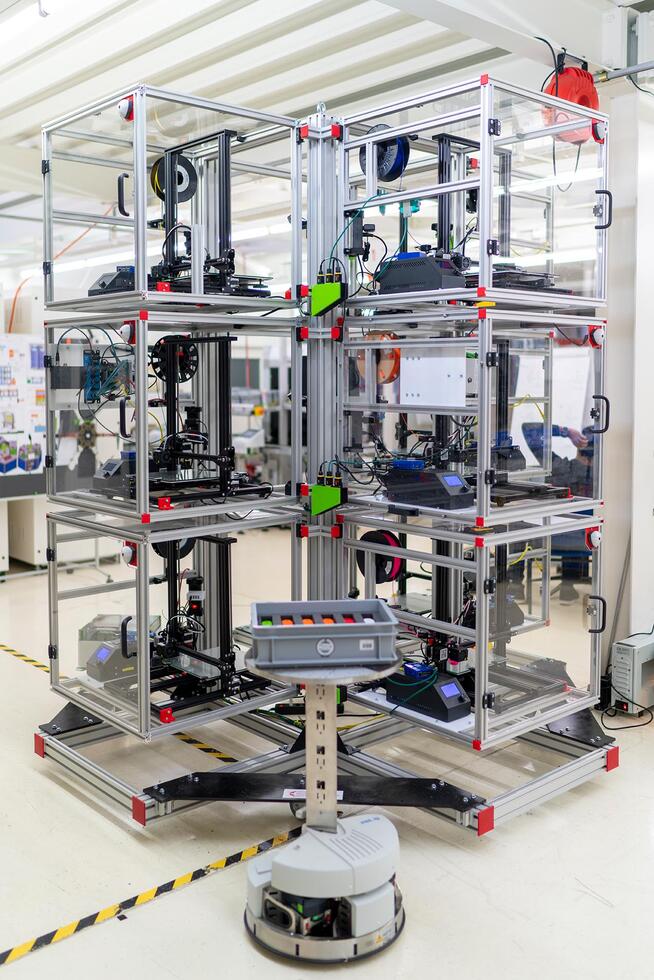
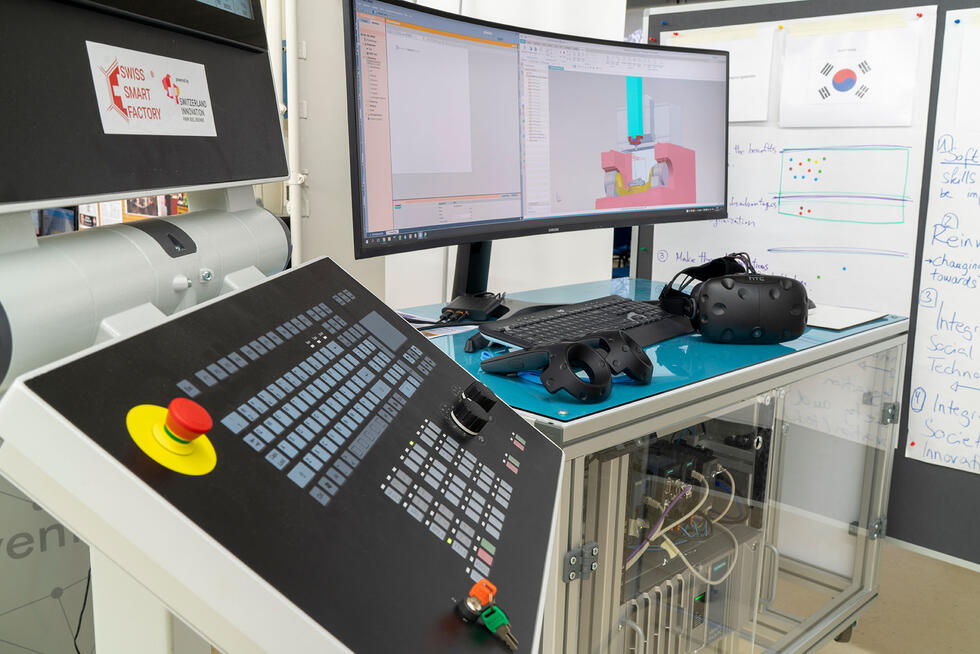
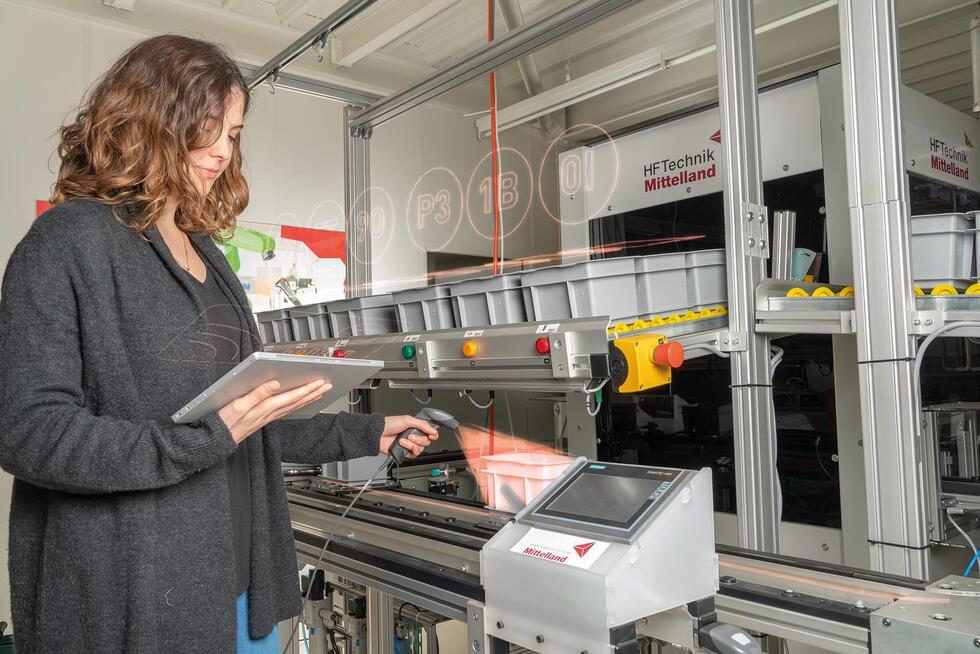
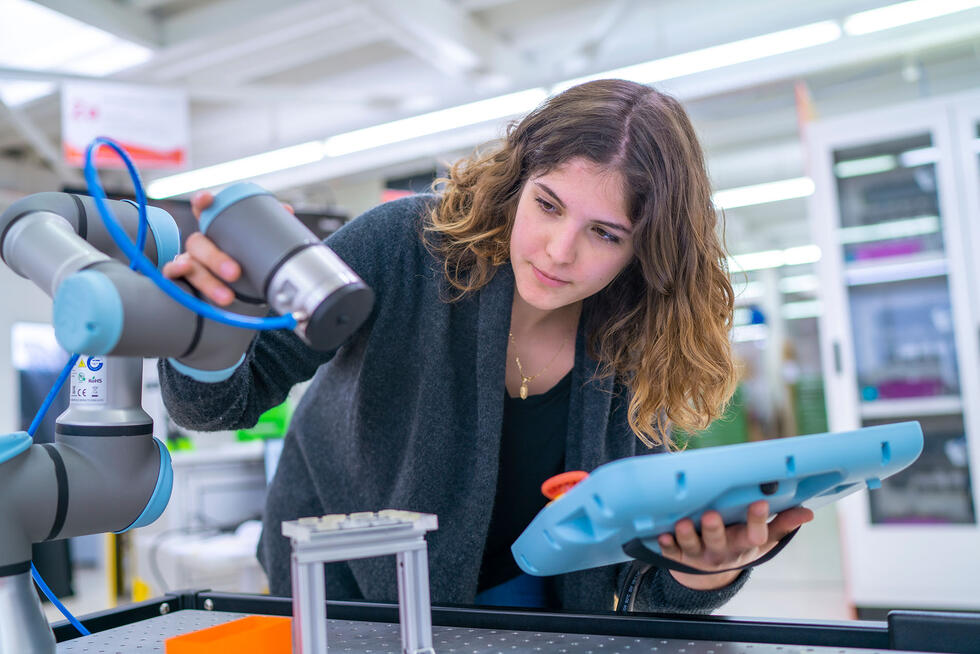
Written by:
Photos: SIPBB