Das Haus aus dem Drucker
Offene Designvorstellungen statt rechtwinkliger Geometrien: Häuser aus dem 3D-Drucker sehen nicht nur anders aus als konventionelle Gebäude. Erste Anbieter aus der Industrie versprechen auch, dass die Technologie schneller und ressourcensparender ist. Stimmt das?
Bunte Spielfiguren, künstliche Hüftgelenke, tödliche Schusswaffen: 3D-Drucker übersetzen beinahe jede digital erdachte Form in die Realität. Und die Technologie wächst seit Jahren rasant. Jetzt könnte sie die Baubranche von Grund auf ändern. Dazu finden weltweit Partner aus Industrie und Wissenschaft zusammen, um ganze Gebäude zu drucken. Auch in der DACH-Region gibt es Modellprojekte: Etwa das „DFAB House“ des Schweizer Forschungsverbunds, das mit Robotern und 3D-Druckern erbaut wurde. In Hausleiten steht Österreichs erster gedruckter Bürokomplex und in Beckum das erste 3D-Druck-Wohnhaus Deutschlands. Die zuständige Bauministerin Ina Scharrenbach sagte bei der Eröffnung, dass es „positiven Druck in der Baubranche erzeugen“ werde.
Gerade erst haben die Vereinten Nationen geschätzt, dass 2021 über ein Drittel der globalen CO2-Emissionen auf die Nutzung und den Bau von Gebäuden zurückging.
Und der ist längst überfällig. Denn die Baubranche muss sich wandeln. Sie ist ein grosser C02 Sünder. Für den Klimawandel. Gerade erst haben die Vereinten Nationen geschätzt, dass 2021 über ein Drittel (37 Prozent) der globalen CO2-Emissionen auf die Nutzung und den Bau von Gebäuden zurückging. Allein die Betonherstellung ist jährlich für rund zehn Prozent verantwortlich. Tendenz steigend.
Dafür ist vor allem eine rasante Urbanisierungsrate verantwortlich. Immer mehr Menschen ziehen vom Land in die Stadt – und brauchen Wohnraum. Dirk Messner, Präsident des deutschen Umweltbundesamtes, sagte vor kurzem: „Die Bevölkerung in urbanen Gebieten wird sich in den nächsten 25 Jahren auf sieben Milliarden Menschen verdoppeln. Würden wir die Gebäude dafür bauen, wie bisher, wäre unser verbliebenes CO2-Budget bis zum 1,5-Grad-Ziel damit verbraucht.“ Nur für diesen Wohnraum. Mobilität, Energie oder sonstige Sektoren sind da noch gar nicht berücksichtigt. Sollte die Baubranche einfach wie bis anhin weitermachen, wird das Ziel des Pariser Klimaabkommens klar verfehlt: den Anstieg der globalen Durchschnittstemperatur auf deutlich unter zwei Grad Celsius über dem vorindustriellen Niveau zu begrenzen.
Runde Ecken – das Markenzeichen
„Die Zeit ist reif für eine Transformation. Immerhin bauen wir heute noch wie vor 60 Jahren“, sagt Christoph Gehlen. Er ist Professor für Werkstoffe und Werkstoffprüfung im Bauwesen an der TU München und setzt große Hoffnungen in den 3D-Hausdruck: „Im Vergleich zum konventionellen Bauen kann Materialeinsatz, und damit CO2-Emissionen und Konstruktionszeit gesenkt werden.“ Konventionelles Bauen heißt: eine Schalung stellen, mit Beton auffüllen und Gitter aus Stahl einsetzen – wie seit Jahrzehnten auf jeder Baustelle. Wenn es nach Gehlen geht, würden dort in Zukunft Gebäude-Drucker zum Einsatz kommen. „Die Technologie könnte schwere Arbeiten übernehmen und damit den Mangel an Arbeitskraft auffangen.“ Und nicht nur das: „Wenn wir die Branche technologisieren, würde das sicherlich für Nachwuchs sorgen“, sagt der 56-Jährige. Denn der schwinde schon lange.
„Im Vergleich zum konventionellen Bauen kann Materialeinsatz, und damit CO2-Emissionen und Konstruktionszeit gesenkt werden.“
Dazu kommt das Versprechen einer maßgeschneiderten Architektur: Dank der Drucker gibt es geometrische Freiheiten. „Wir können neue Designs und Formenvielfalt realisieren“, sagt Gehlen und spielt damit auf die „runden Ecken“ an – die Markenzeichen gedruckter Gebäude. Sie entstehen, weil der zähflüssige Baustoff gleichmäßig verdruckt werden muss. Sonst geraten die Mauern unterschiedlich dick. Um das zu vermeiden, werden Ecken zu engen Kurven.
Am meisten wird derzeit das ablegende Verfahren, die Extrusion, genutzt. Die funktioniert so (es gibt auch andere, siehe Infobox 2): Von einer frei im Raum beweglichen Achse hängt eine Düse. Hindurch fließt auf Knopfdruck eine spezielle Betonmischung. Was wie graue Zahnpasta aussieht, erhärtet schnell und wächst Schicht für Schicht zu einer Mauer. Besonders ist, dass jede Schicht aus einem anderen Material, mit anderen Eigenschaften, bestehen kann. Die derzeit meistgenutzte Maschine kann Gebäude mit bis zu zehn Metern Höhe und knapp 15 Metern Breite erstellen. Die Länge ist flexibel. Das liegt daran, dass der Aufbau mit der Düse, sozusagen das Druckergehäuse, modular erweitert werden kann. Die Düse druckt eine Schicht Wand mit bis zu 50 Zentimeter pro Sekunde. Das klingt schnell, die Netto-Druckzeit macht in den Pilotprojekten aber nur einen Bruchteil aus. Viel länger dauert es, die Baustelle vorzubereiten, den Drucker aufzubauen, die Maschinen zu warten und Fehler zu beheben, was nur wenige Experten mit Spezialwissen können.
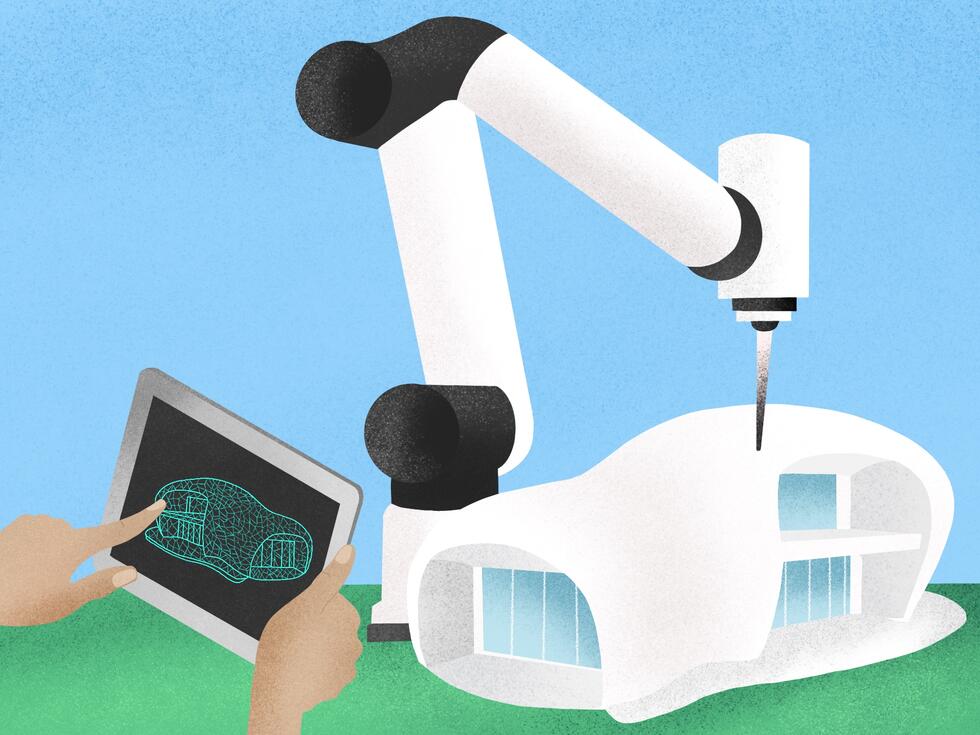
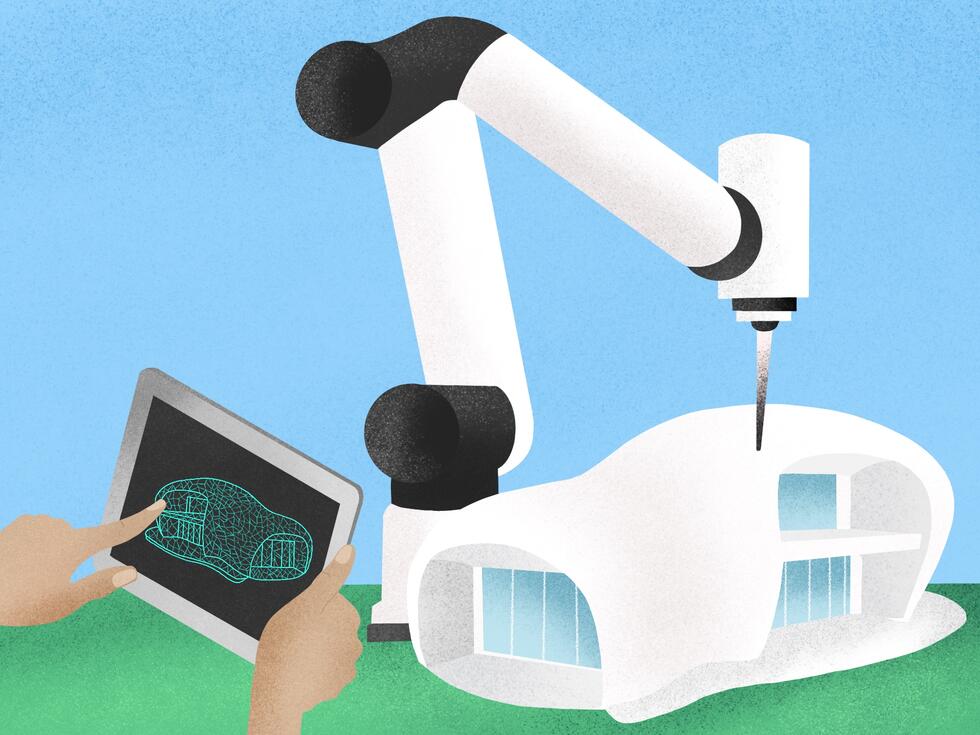
Was kann gedruckter Beton?
Gehlen ist trotzdem Fürsprecher des Hausdrucks – und langjähriger Experte. Er hat das 3D-Haus in Beckum auf Seiten der Wissenschaft begleitet und kann deshalb wie kaum ein Zweiter erklären, was die Technologie kann. Seit 2013 tüftelt er mit seinem Team in Münchner Uni-Werkstätten daran, Beton druckbar zu machen. Konventionelle Produkte, das stellten sie schnell fest, eigneten sich nicht. Dennoch sollte auch für den Druckbeton Zement die Basis bilden, da dieser überall verfügbar ist. „Anfangs haben wir aussergewöhnliche Ideen verfolgt.“ Beispielsweise haben sie Holzchips beigemengt. Mit mäßigem Erfolg. „Die bekannten Unverträglichkeiten liessen sich nicht in ausreichendem Masse kontrollieren.“ Etwa, dass Inhaltsstoffe im organischen Holz das Aushärten des mineralischen Zements verhindern. Mit der Zeit aber fanden sie Rezepte, die den Beton nicht nur ausreichend verflüssigen und pumpbar machen, damit er durch den Druckschlauch gelangt und kurze Zeit später dennoch formstabil und schnelltrockend ist.
„Die bekannten Unverträglichkeiten liessen sich nicht in ausreichendem Masse kontrollieren“
Bei dem Haus in Beckum konnte Gehlen zeigen, was gedruckter Beton leisten kann. „Wir haben die Zulassungsversuche für die Bauaufsichtsbehörde durchgeführt“, sagt er. Sein Team führte beispielsweise Studien zur Witterungsbeständigkeit durch. Dafür setzte es gedruckte Betonkörper extremen Bedingungen aus. „Wir haben sie einer zeitraffenden Frost- und Tau-Beanspruchung unterworfen“, sagt Gehlen. Das heißt: Die Betonkörper sogen sich in einem Wasserbad voll, wurden anschliessend eingefroren und wieder aufgetaut. Jahreszeiten im Schnelldurchlauf. Dann haben sie mithilfe von Mikroskopen und Ultraschallgeräten geschaut: Wie ist der Baustoff gealtert? Kaum.
Der Druckbeton bestand auch alle statischen Prüfungen. Jedes einzelne Bauteil ist, so heißt das, ausreichend „standsicher“. Dabei befürchtete selbst Gehlen, dass im Vergleich zu konventionellen Steinmauern gedruckte Wände viel weniger Belastung aushalten würden. Die Herausforderung liegt im Timing: Weil Lage auf Lage gedruckt wird, entsteht dazwischen eine Fuge. Fließt der Beton zu langsam, entstehen „Cold Joints“. Kalte Fugen. Dann haften die aufeinanderliegenden Betonstränge nicht mehr so gut. Ein neuer Strang muss auf einen „frischen“ aufgedruckt werden – aber nicht zu schnell. Sonst verformt sich der darunterliegende instabile Beton. In Beckum wurden neue Schichten nach sieben bis zwölf Minuten aufgetragen, so gab es keine Cold Joints. Im Vergleich erreichen die gedruckten Mauern rund 80 Prozent der Standfestigkeit konventioneller Betonwände.
„Der Hausdruck ist nicht die Lösung für die Baubranche“
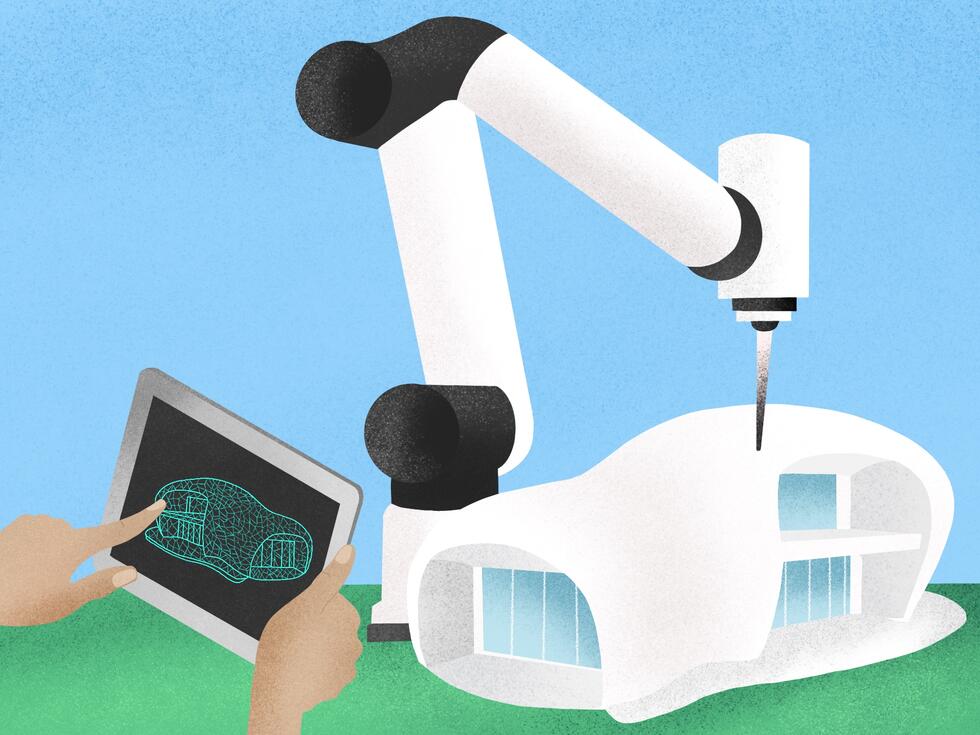
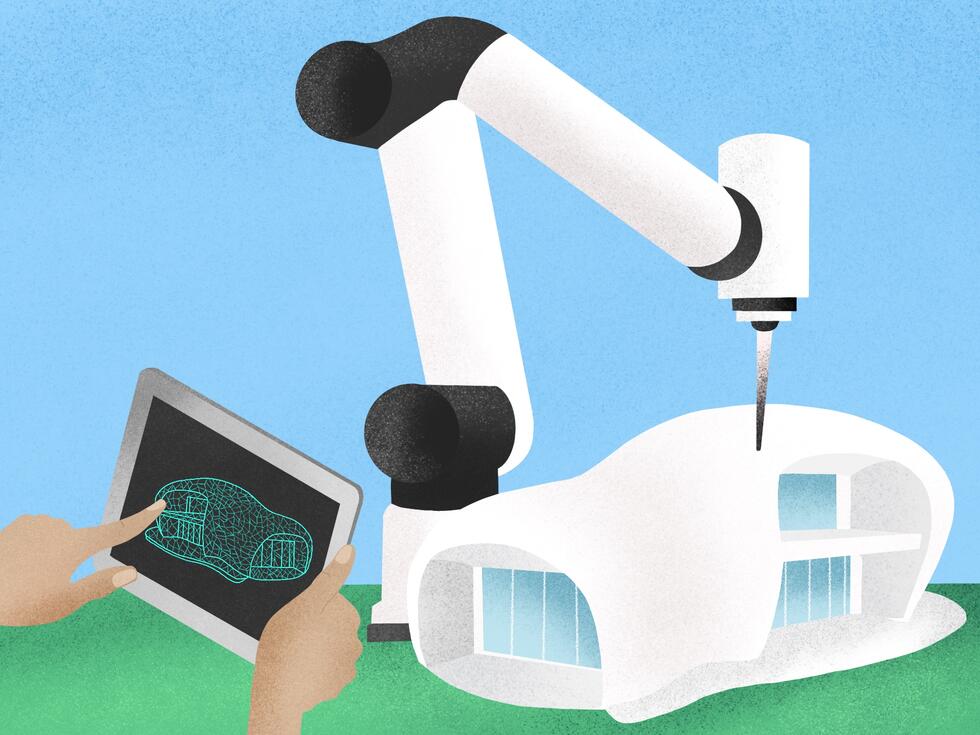
Lücken mit Funktion
Gleichzeitig können gedruckte Wände mehr. „Weil wir etwa Resonanzkörper, die Schall schlucken, in die Oberfläche drucken können“, sagt Gehlen. „Oder wir sparen in den Wänden funktionale Hohlräume aus.“ Hindurch könnten leichter Medien verlegt oder Warmluft, die das Gebäude heizt, geleitet werden. Der größte Vorteil: Besteht die Wand aus nur einem Material, kann sie leichter recycelt werden. Heute bestehen Wände aus verklebten Materialsandwiches. Jede Lage hat eine andere Funktion. Deshalb können die Bauteile nur mit viel Aufwand und Geld wieder getrennt werden – in der Praxis passiert das fast nicht. „Es wäre ein Beitrag zur Nachhaltigkeit, wenn wir sortenrein gedruckte Wände in einen Bau-Kreislauf zurückführen“, sagt Gehlen.
Den größten Beitrag des Hausdrucks zur Nachhaltigkeit sieht der Werkstoffprofessor aber hierin: „Wir können eine Menge Material an Decken und Wänden sparen. Weil wir nur drucken, was wir brauchen.“ In konventionellen Gebäuden seien Mauern überall gleich dick. Dabei müsse das für die Traglast nicht sein. „Deshalb gehen Ressourcen verloren. Der 3D-Druck lässt uns viel gezielter bauen.“ Das spare bis zu 50 Prozent Material, bei manchen Bauteilen mehr. Selbst, wenn alle Bauteile nur ein wenig schlanker ausfielen, ergebe das einen großen Hebel. „Häuser, Tunnel, Brücken: Wenn man überall 30 Prozent abzieht, ist das erheblich“, sagt Gehlen.
„Es wird sicher nicht zu einem vollständigen Ersatz des konventionellen Bauens kommen.“
Trotz allem: Der Hausdruck ist nicht die Lösung für die Baubranche. Zumindest noch nicht. In diese Richtung weist auch die Bewertung auf der „Technology Readiness Skala“ (siehe Infobox 1): von 9 Stufen steht die noch junge Technologie zwischen 6 und 7. Übersetzt heißt das, der Hausdruck funktioniert „im tatsächlichen Einsatzgebiet“ und die Maschinen „ragen an ein fertiges Produkt heran“. Auch eine Übersichtsarbeit zu acht Modellprojekten in acht Ländern kommt zu einem ähnlichen Ergebnis. Da heißt es: „Zwar nimmt die Zahl an Modellprojekten schnell zu, sie verfolgen bislang aber eher das Ziel, Potenziale aufzuzeigen und nicht unbedingt, sie auch zu erreichen.“ Es sind diese (theoretischen) Möglichkeiten, die auch Gehlen überzeugen. Er sagt, man werde – digital unterstützt – schlanker, schneller, abwechslungsreicher und vielleicht auch billiger bauen können. „Das macht den Hausdruck zur Zukunftstechnologie.“ Aber: Es werde „sicher nicht zu einem vollständigen Ersatz des konventionellen Bauens“ kommen.
Und dann gibt es da noch ein weiteres Problem: den Baustoff. Flüssigbeton beruht bisher auf sehr feinkörnigen Rezepturen, statt Kies braucht er Sand. Je kleiner das Korn ist, desto mehr Leim muss eingesetzt werden. „Und der Leim besteht aus Wasser und viel Zement. Deshalb ist der CO2-Ausstoß immer noch viel zu hoch“, sagt Gehlen. „Wenn ich jetzt eine Bewertung der Technologie abgeben müsste, würde die nicht schön ausfallen.“ Er sehe aber riesiges Potenzial und man werde in der Forschung alles daransetzen, dass Emissionen sinken oder ganz vermieden werden könnten. „Bislang ist das aber nicht so“, sagt Gehlen.


Nicht mehr als „eine nette Gestaltgebung“
Zu einem ähnlichen Ergebnis kommt auch Annette Hillebrandt. Sie hat den Lehrstuhl für Baukonstruktion, Entwurf und Materialkunde an der Uni Wuppertal inne und erforscht dort Kreislaufpotenziale im Hochbau. An den aktuellen Hausdruck-Projekten ist sie nicht beteiligt, beobachtet die Entwicklung aber. Für sie sind 3D-Häuser wegen des viel zu hohen Zementanteils im Flüssigbeton noch keine nachhaltige Lösung. „Es gibt aber auch Holz-3D-Druck. Dort wird als Bindemittel allerdings zur Zeit größtenteils Kunststoff als Bindemittel zugesetzt, der eine Kreislauffähigkeit, also spätere Kompostierung verhindert“, erklärt sie. Deshalb könne sie der Technologie, außer einer netten Gestaltgebung, nichts abgewinnen.
Sie führt noch zwei weitere Punkte an. Der erste: „Gegenüber rechtwinkligen, modularen und vorgefertigten Skelettbauten verschwendet die geschwungene Form Ressourcen. Denn sie ist schlecht umnutzbar, zu determiniert, zu unflexibel.“
Der zweite Grund greift tiefer: Hillebrandt hält Neubau generell für nicht nachhaltig. Auf Deutschland bezogen sagt sie: „Wir haben stagnierende Bevölkerungszahlen. Deshalb sollten wir mit dem bestehenden Gebäudebestand auskommen.“ Klar, der könne umgebaut oder herausgeputzt werden. Aber: „Wir haben nur noch ein kleines CO2-Budget, wenn wir die Klimaziele einhalten und die Erderwärmung auf 1,5 oder 2 Grad eindämmen wollen.“ Da sei jedes unnötige Kilogramm CO2 zu viel. Sie sagt: „Ja, 3D-Druck ist hübsch. Aber eine Lösung in dieser Zeit des Klimawandels und der immer rarer werdenden Rohstoffe wird er erst, wenn Altmaterial aus Holz oder Reststoffe verdruckt und mit Naturharzen gebunden werden.“ Dann allerdings, so befürchtet sie, könnten auch Umweltgifte beigemengt werden, um die Häuser beispielsweise vor Pilzbefall oder Käferfraß zu schützen. Damit wäre aber die Kreislauffähigkeit wieder zerstört.
Infobox 1
In einer Übersichtsarbeit wurden unterschiedliche Bauprojekte aus acht Ländern untersucht, darunter das Haus in Beckum. Laut den Autoren und Autorinnen hat der dreidimensionale Hausdruck mittlerweile eine 6 bis 7 auf der „Technology Readiness Level“ (TRL)-Skala. Die reicht von 1 bis 9 und beurteilt so die Reife einer Technologie. Ursprünglich entwickelt wurde sie von der US-Raumfahrtbehörde NASA, um die Frage zu beantworten: Ist eine Entwicklung zuverlässig genug, um in Raketen und Satelliten eingesetzt zu werden? Mittlerweile wird die Skala aber in vielen Forschungsfeldern eingesetzt, um den Entwicklungsstand einer Technologie von der Grundlage bis zum fertigen Produkt zu beschreiben. Level 6 bedeutet „Prototyp in Einsatzumgebung“, Level 7 „Prototyp im Einsatz“. Das heißt, der 3D-Druck konnte zeigen, dass er „im tatsächlichen Einsatzgebiet funktioniert“ und an ein fertiges Produkt heranragt. Dabei ist der Schritt von Level 6 zu 7 ein wichtiger, weil er die Forschung & Entwicklung mit der Pilotanwendung verbindet und damit raus aus dem Labor und rein in die Anwendung „auf dem Feld“ führt.
Infobox 2
Neben der Extrusion wird auch am „Shotcrete“-Verfahren geforscht. Dabei wird Beton nicht durch eine Düse gedrückt, sondern mit hohem Druck geschossen. Das erhöht die Baugeschwindigkeit und sorgt für eine bessere Vermischung der Lagen. Auch muss die Düse nicht mehr über der Mauer schweben, sie kann von der Seite Beton aufbringen. Oberflächen werden allerdings noch unebener. Ein weiteres Verfahren, das entwickelt wird, ist der Partikelbett-3D-Druck. Es hat den Vorteil, dass Strukturen innerhalb des Druckraums frei entstehen können. Der wird dafür mit einem Sandbett gefüllt. Gewünschte Stellen werden, wie mit einem Tintenstrahldrucker, mit einer Suspension aus Wasser und Zement verleimt. Dort verfestigt sich das Partikelbett. Gedruckt wird Schicht für Schicht. Der Vorteil: Ungebundene Partikel bleiben liegen und dienen als Stützstruktur für den Druck. Eine andere Herangehensweise ist es, mit nachhaltigen Materialien zu drucken. Ein Beispiel dafür ist Tecla, ein Gebäude aus Materialien, die ausschließlich an Ort und Stelle des Gebäudes gesammelt werden. Die Firma wirbt damit, dass so CO2-neutrale Lehmhütten aus vollständig wiederverwertbaren Materialien entstehen, die sich an jedes Klima und jeden Kontext anpassen.
Quellen:
https://www.youtube.com/watch?v=XhPrhlosmDo
https://www.unep.org/resources/publication/2022-global-status-report-buildings-and-construction
https://youtu.be/BNk3m8Y0aV8?t=3413
https://www.mae.ed.tum.de/cbm/ueber-uns/geschaeftsleitung/institutsleitung/gehlen-christoph/
„The realities of additively manufactured concrete structures in practice“
https://www.3dwasp.com/en/3d-printed-house-tecla/